Running an eCommerce operation comes with its fair share of challenges, and one of the most frustrating issues we faced running our 3PL business was packers selecting the wrong packaging at the packing station. They often opted for packaging that was easier to reach or more convenient for packing.
As warehouse operators, we understand that warehouse operatives love a shortcut but these can lead to significant problems, and it’s not always clear to warehouse staff how these choices can impact costs and customer satisfaction. This might be manageable when you have a small team shipping out a few orders, but when you’re dealing with tens of thousands of orders—with multiple product sizes and packaging options to choose from, and staff coming in and out, especially temporary workers—it can quickly become chaotic and costly.
Without proper guidance, mistakes are bound to slip through the cracks, resulting in inefficiencies that affect both the bottom line, overall customer experience and cause issues like:
- Impact on Margins: Larger boxes are more expensive, and while it makes sense to scale up packaging for larger orders where revenue can absorb the cost, sending out a single item in an unnecessarily large, costly box eats into margins. Over time, these seemingly small choices add up and can significantly affect profitability.
- Volumetric Misalignment: When shipping parcels, especially internationally, oversized boxes can lead to higher shipping costs due to volumetric weight calculations. You end up paying to ship air, which is a huge waste of money!
- The 'Amazon Problem': We've all been that customer who orders a pencil and receives it in a box that looks like it should hold a suitcase. That screams wastefulness and shows a lack of care, which is not the impression you want to leave with customers.
- Increased Handling and Storage Costs: Using the wrong packaging can also mean higher handling and storage costs because of the extra space needed for inefficient solutions.
Our approach to tackling this issue revolves around Pimento’s innovative box containerisation algorithm, which ensures that packers select the right box every single time.
Here's how it works:
1 - Accurately input each product's dimensions in the system.
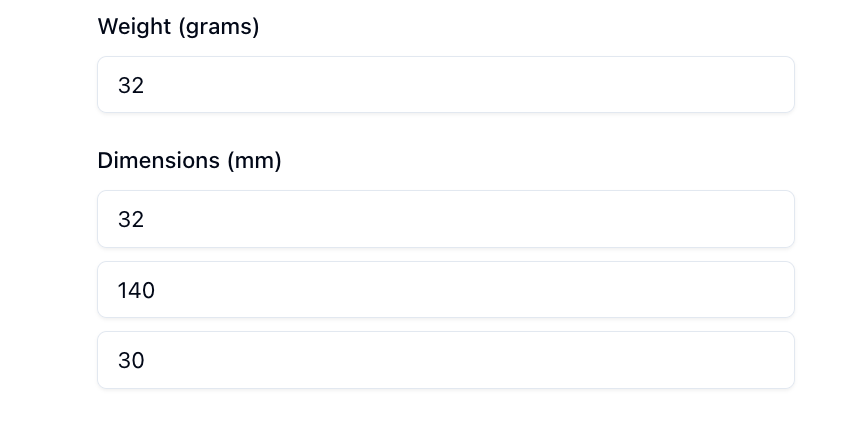
2 - Add your packaging options to the system, including the internal dimensions and weight.
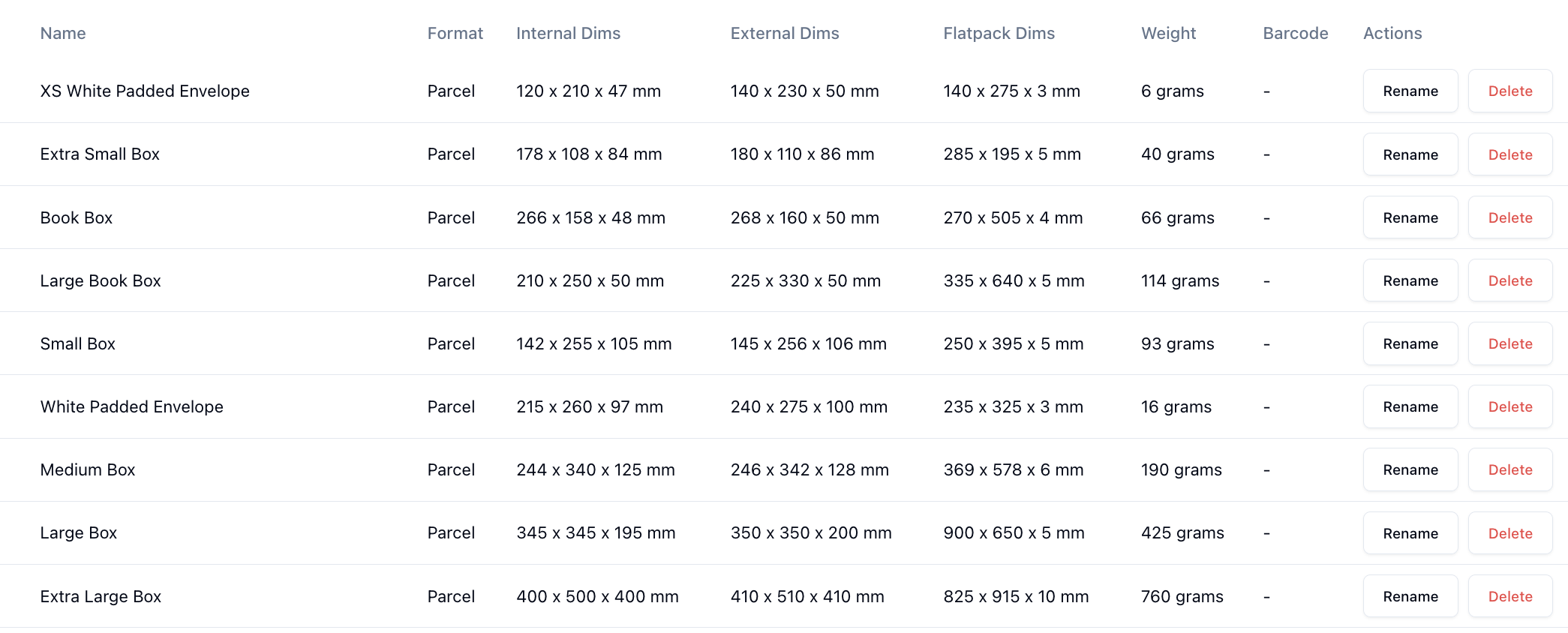
3 - Set specific rules to determine which packaging should be used for different orders. This could be based on size of order, brand, products, shipping service and more.
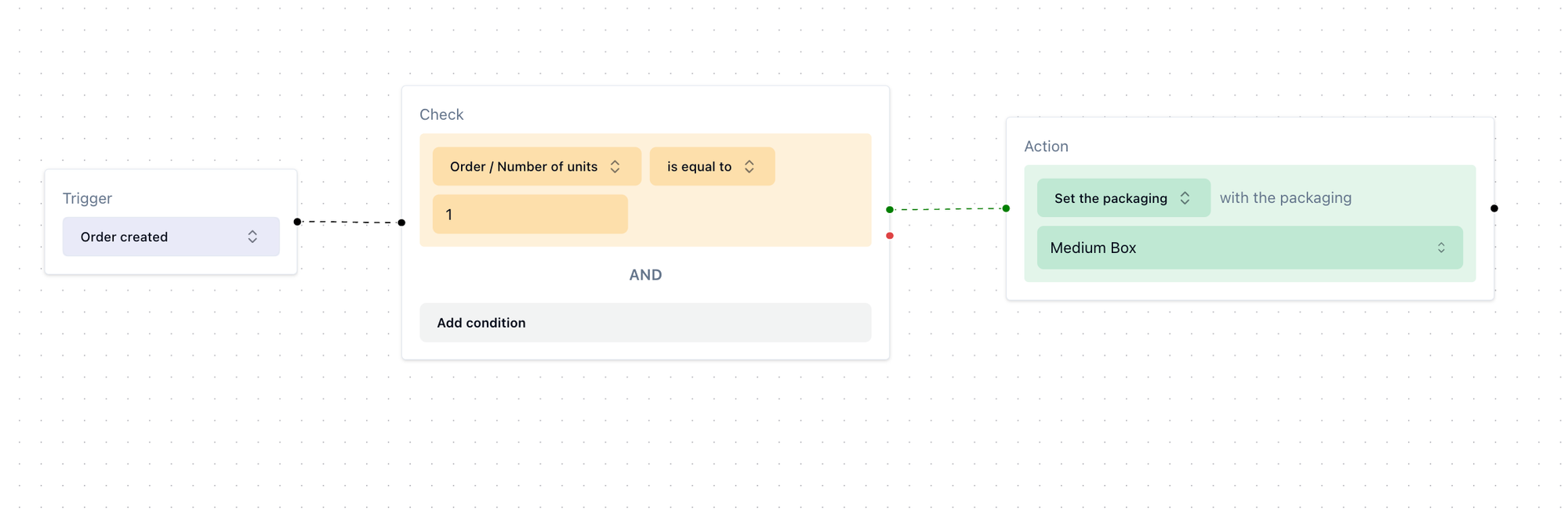
4 - When an order comes through, the system checks the product dimensions and other criteria like if it's clothing, Pimento understands it can be folded and how and as a result applies the correct packaging based on your rules.
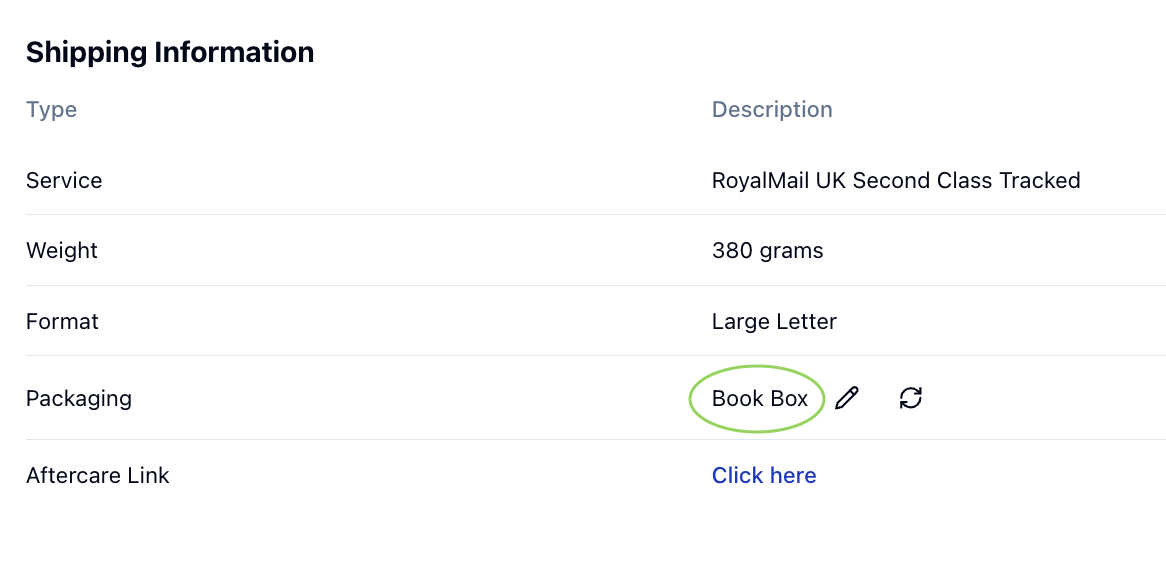
5 - Before a parcel heads out the door, you can turn on the weight check feature. If the weight is heavier than expected, Pimento will flag it assuming the incorrect box was used, ensuring the right box is selected before issuing a label.
As touched on above, Pimento adapts to various packaging needs, considering factors like clothes folding and mailer bag flexibility. It even accounts for void fill, ensuring parcels are packed securely without unnecessary space. The system boasts an impressive accuracy rate of 100% in selecting the correct box, eliminating the likelihood of incorrect box selection.
By ensuring the correct box is used, Pimento helps reduce shipping costs and improve the overall packing process. It’s all about making operations smoother and creating a better experience for both packers and customers alike.
If you want to learn more about this feature or just want to experience an overall demo, reach out to me at sait@getpimento.com. I'd love to show you more and answer questions you may have.